BLOG | Physical test data removes guesswork from masonry support specification
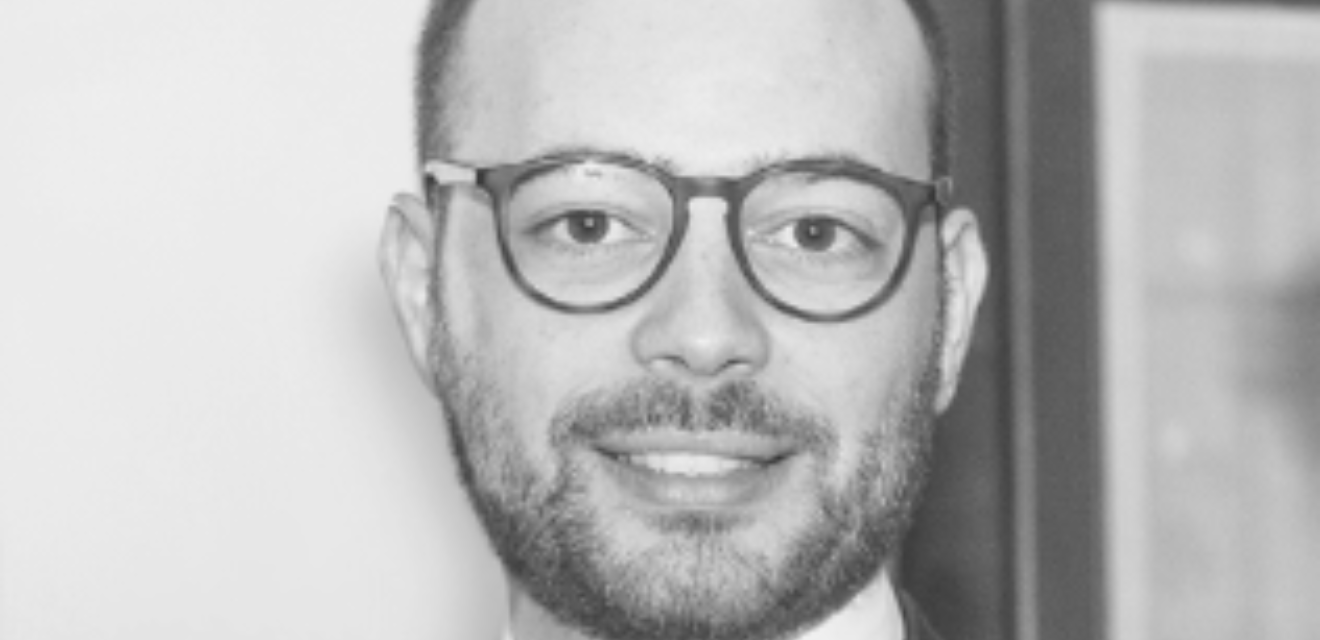
Masonry support systems have been crucial to improvements in both brick building design and safety. However, until IG Masonry Support drove the development of a new and reliable testing regime, assumption played a large part in the specification of ancillary masonry products for UK projects. So, how does IG Masonry Support’s testing system work, and why is there no uniform regulation regarding masonry support products? Emanuele Scarabino, IG Masonry Support’s R&D Manager explains.
It’s very difficult to create a design code for masonry support products that can be shared, acknowledged and absorbed by other countries. In Italy and Spain, for example, masonry soffit systems and the like are not widely used due to brick not featuring as prominently within the architecture. Whilst in Britain and Ireland, where brick facades have been prevalent throughout the built environment for many decades, there has been no compelling reason to introduce regulatory testing guidelines because there have been no major issues with masonry support products in buildings.
Consistency is very important when it comes to the testing and design of building products. Without it, assessment methods and maintenance statements are a thing of individual responsibility. Whilst this approach might satisfy the requirements of one structural engineer, it might not be appropriate for another. Without uniform testing data in place, it leads to assumptions being made on a building product’s projected performance. The absence of such detail could lead to incorrect product specification dramatically increasing the risk of failure.
At IG Masonry Support, we developed a physical testing method to ensure the assumptions we made on our products’ performance were correct. In the five years since we devised the process, we’ve carried out more than 1,000 tests. It means if a consultancy engineer enquires as to why a particular masonry support system needs to allow for a specific deflection, we have the data to support our decision.
Test process
Our physical testing method was developed over several months. It’s carried out using a masonry support testing rig, a 2m x 3m steel structure that simulates the strength and response of a 10-storey building. Assessments take place at Queen’s University Belfast Laboratory using UKAS-accredited machinery. Such facilities are ideal for fulfilling IG Masonry Support’s philosophy: ‘test as much as possible in order to prove the assumptions you make’.
In terms of how we apply loads to assess the masonry support’s ‘real-life’ impact via our testing rig, we undertook finite element analysis (FEA) using three different software, the main two being SolidWorks and ANSYS. Through FEA, we identified how to replicate bricks’ weight and density and the optimum way to load them to the testing rig’s top shelf.
The process became the blueprint for hundreds of assessments, the results of which were included in a paper published in conjunction with Queen’s University, Belfast: “Experimental Study of Vertical Deflection on Bracket-Angle Stainless Steel Masonry Support Systems”. To our knowledge it is the first testing-based paper in relation to masonry support. Data and testing images included within the paper have since been shared at conferences hosted by Queen’s University Belfast and the Institution of Structural Engineers.
Software development
The need to develop products and processes that help improve building standards continues to drive us. Hence, we developed bespoke software which stores all of our test results on a single database. We designed the software to be capable of creating the ideal masonry support solution based on a set of key values including wall cavity, concrete slab height and brick density. As well as giving an accurate prediction of our masonry support system deflection, the software is capable of designing all of the other system values around it – the support’s stainless-steel thickness, for example. Will a 5mm or 4mm angle provide enough capacity? Our software will answer that question too, based on a list of stress checks that also include brackets and a range of general fixings.
The software provides a printout of the design specification of each IG Masonry Support product. From deflection estimation to fixing design, clients are provided with an accurate, reassuring summary of the system’s performance backed by test data. Industry reaction has been very positive about our innovation in masonry support test methodology, with associate engineering consultants telling us the system has instilled an additional layer of trust in IG Masonry Support products, compared to our competitors. But our innovation continues. Since we originated the software in 2018, we have carried out more than 50 updates in order to adapt and refine its performance.
IG Masonry Support’s software package benefits our engineers by bringing uniformity to the masonry support design process. It also helps our clients, as it not only selects the best system from a design perspective, it chooses the most cost-effective solution from all the available structurally-safe masonry support designs. Furthermore, the software package is very good news for the construction industry. It proves that our masonry support products are not assigned on assumptions but they have been physically tested setting the foundation for a process that can only improve building standards in terms of safety and design.
Request CPD Presentation
Gain your CPD points by requesting a Continuous Professional Development presentation on IG Masonry Support solutions.
Request CPD